Neoprene
Neoprene is the common trade name of the chloroprene elastomer developed by Dupont in 1931. According to the Technical Handbook for Elastomeric Roll Covering, “there are no characteristics to which chloroprene is superior to all other special purpose rubbers. Its importance is not due to excellence in a single property but to a combination of technically essential properties…” Neoprene is used in the roll industry due to its average strength in several desirable categories.
Why Choose Neoprene Rubber?
- Chemical Resistance: Neoprene stands up to oils, solvents, and chemicals, making it ideal for industrial applications.
- Heat & Weather Resistance: With a broad temperature range (-40°F to 275°F), neoprene performs well in extreme conditions.
- Tear & Abrasion Resistance: Neoprene rubber rollers and molded parts are long-lasting and can withstand high-friction environments.
- Versatility: From conveyor systems to printing presses, neoprene rubber components are used across industries.

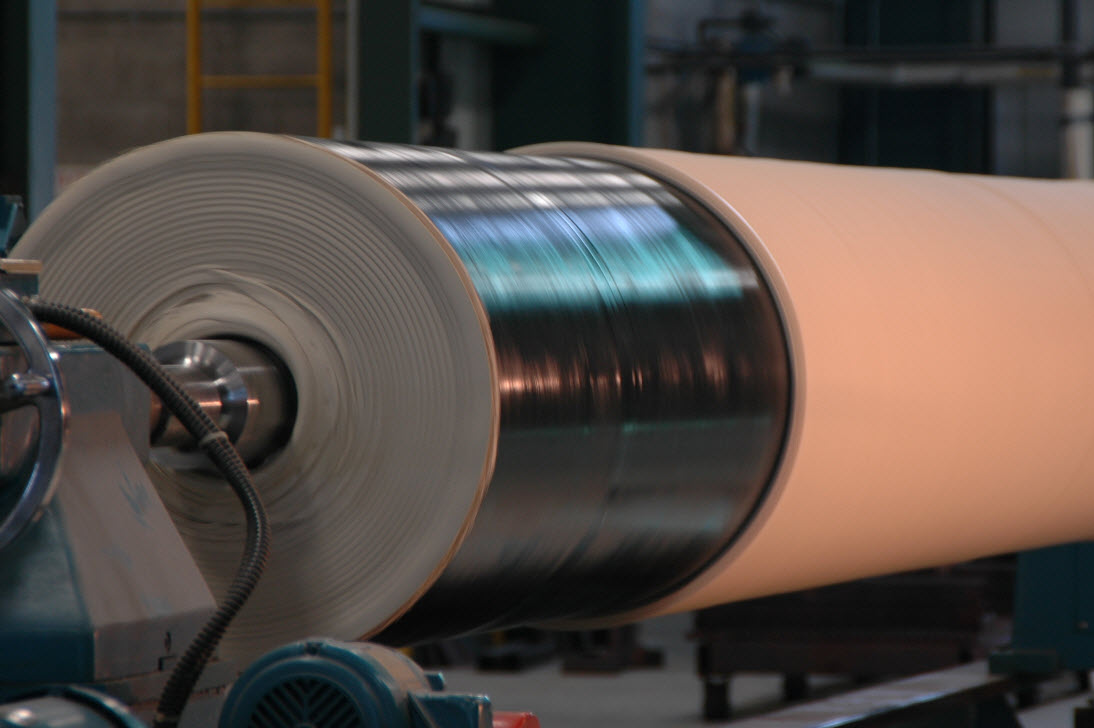
Types of Neoprene Rubber Rollers
Understanding the different types of neoprene rubber rollers can help you select the best option for your specific application.
-
Industrial Conveyor Rollers
- Used in material handling and automated production lines
- Designed for durability and high-speed applications
- Available in custom sizes and durometers for different load capacities
-
Printing & Coating Rollers
- Essential for precise ink or coating application
- Neoprene offers a consistent grip and smooth transfer
- Resistant to solvents and inks, making it ideal for long-term use
-
Laminating & Packaging Rollers
- Ensures even pressure distribution for quality lamination
- Resistant to adhesives and heat exposure
- Custom formulations available for specialized applications
Key Considerations When Buying Neoprene Rubber Rollers
Before purchasing neoprene rollers, consider these critical factors:
Material Hardness (Durometer)
The durometer (hardness) of neoprene rubber affects its performance. Lower durometer rollers (soft) provide better grip and cushioning, while higher durometer rollers (hard) offer greater precision and wear resistance.
- 40-50A Durometer: Ideal for applications requiring flexibility and grip
- 60-70A Durometer: A balanced option for general industrial use
- 80-90A Durometer: Best for high-pressure and precision applications
Surface Finish & Coating
- Smooth rollers: Best for printing and coating applications
- Textured rollers: Provide additional grip for conveyor and packaging systems
- Coated rollers: Optional coatings like Teflon improve performance in specialty applications
Core Material
Neoprene rollers typically have metal or composite cores for structural integrity. Consider factors like:
- Aluminum cores for lightweight applications
- Steel cores for heavy-duty use
- Fiberglass cores for non-conductive or corrosion-resistant applications

Partner with Rol-Tec for Neoprene Rubber Rollers
Looking for high-quality neoprene rubber rollers and molded parts? Contact a trusted manufacturer to discuss your specific requirements and find the perfect solution for your business.
Neoprene vs. Nitrile Properties
Rubber Compound |
Nitrile | Neoprene |
BN | NE | |
Physical Properties | ||
Hardness Range Shore A | 20-95 | 25-95 |
Hardness Range P&J | 0-200 | 10-300 |
Abrasion Resistance | 3 | 3 |
Tear Resistance | 3 | 3 |
Load Bearing | 4 | 4 |
Hysteresis | 2 | 3 |
Resistance to Denting | 3 | 2 |
Maximum Service Temperature (C/F) | 121/250 | 121/250 |
Ozone Resistance | 1 | 3 |
Resiliency | 3 | 2 |
Solvent Resistance | ||
Acids | 2 | 3 |
Caustics | 3 | 3 |
Paraffinic Hydrocarbons | 5 | 3 |
Aromatic Hydrocarbons | 3 | 2 |
Chlorinated Hydrocarbons | 1 | 1 |
Water | 4 | 3 |
Ketones | 2 | 3 |
Alcohols | 5 | 3 |
Esters | 1 | 3 |
Recommended Applications | ||
Coating/Varnishing | ● | ● |
Embossing | ● | |
Flexography | ● | ● |
Laminating | ● | ● |
Laser Engraving | ||
Metal Decorating | ● | |
Offset Printing | ||
Paper Making Industry | ● | |
Plastics | ||
Plate Processors | ● | |
Steel Mill Rollers | ● | ● |
Textile Rollers | ||
Wood Industry | ● | ● |